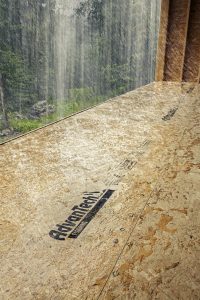
Advancements in framing and insulation coupled with a desire to build tighter, more energy efficient, durable homes has created a lot of consideration in evolving wall assemblies. But as finishing materials become more sophisticated, there may be a need to look down — to the flooring system.
If I asked you to think about vapor control, it’s likely you would immediately think of the wall assembly, dew points and moisture migration,” said Chris Vegas, AdvanTech® technology director at Huber Engineered Woods. “But it can be equally important to think about moisture and vapor control layers with the floor assembly. After all, depending on the project location and type of construction, you will experience similar air, moisture and energy movement through the floor system.”
In certain geographies, like coastal areas, moisture should be an even greater consideration due to the field service conditions of these assemblies. For example, if you are designing or building a home on stilts or with a crawl space, you’ll want to pay extra attention to moisture concerns for the floor system. As with the wall system, this means managing bulk water, air flow and then vapor.
Think of the floor as a full assembly, as opposed to the subfloor and finished materials as separate parts.
Has the bulk water been managed?
As always, you should first make sure that there isn’t an opportunity for bulk water to reach or build up on the floor system. In coastal areas, this typically means raising the floor system above the flood plain to account for potential storms and flooding. For houses with crawl spaces, bulk water is managed by proper grading to allow for drainage away from the foundation. In the case of vented crawlspaces, cross ventilation will help to maintain acceptable relative humidity levels.
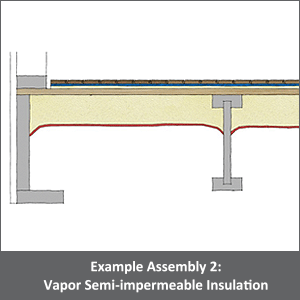
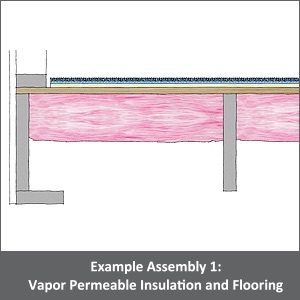
How is air flowing in and around the structure?
The summer months in the southeast and other coastal areas can be brutal when it comes to humidity. In these areas where hot temperatures are paired with prolonged periods of high relative humidity, builders should consider the flow of air—and subsequently humidity—into crawlspaces, floor cavities of stilt-built homes, and even unfinished basements.
“The warmer the air, the more moisture it can hold. So, when air flows into a cooler place like a shaded crawl space adjacent to air conditioning, it has the potential to condense on the underside of the subflooring, especially if the home is kept at lower temperatures,” said Vegas.
This movement of water vapor from outdoors to indoors—or, inward vapor drive—can cause issues if not properly managed. It’s important to take all components of the flooring system into consideration when determining the most appropriate, and moisture-resistant, flooring assembly for your build.
How can vapor concerns be addressed? And, what role does finished flooring play?
Luxury flooring alternatives like vinyl tile and vinyl planks have gained popularity. However, vinyl products are vapor barriers, meaning they are impermeable and would not allow for the floor system to dry in both directions.
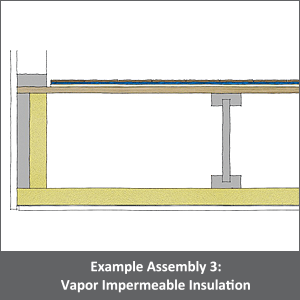
One method for limiting condensation build up with the use of a vented crawl space is to add insulation under the subfloor. Just be sure to choose the proper insulation to fit your geography and finished floor system. It is pertinent to take into account the permeance of the finish floor when designing the system to allow for proper drying. For example: A home built over a vented crawl space in the Southeast U.S. would need insulation that is less permeable than the finish floor, such as closed cell foam used with hardwood flooring.
Overall, it’s important to keep a few things in mind when it comes to floor systems:
Understand the environments in which you build. Take relative humidity and large temperature swings into consideration.
Think of the floor as a full assembly, as opposed to the subfloor and finished materials as separate parts. Know the vapor permeance of all products in the assembly to avoid a double vapor barrier.
Air sealing is critical. Control the movement of air, and you control the movement of moist air which can cause condensation build up in the first place. If crawlspaces are necessary, consider building over a closed and conditioned space.
Lastly, make sure you’re installing subflooring that will give you the best moisture-resistance during construction exposure. “One of the reasons builders have chosen AdvanTech subflooring for decades in humid, or storm-prone areas is its ability to maintain its strength, stiffness and fastener-holding properties even through wetting and drying cycles,” said Vegas.