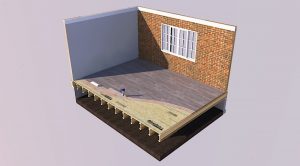
Regardless of the location or build season, today’s interior built environments have a common design goal to create microenvironments that are humidity and temperature controlled. Generally speaking, Americans have come to expect a standard of residential interiors that remain between 68-75 degrees, on average, across all US climate zones. In response, all building assemblies adjust and adapt to find better balance with the surrounding natural environment. But when the outdoor environment is radically different than the indoors, such as that in the high humidity, high heat climate of the American South, it creates a constant assault on the building envelope. As nature attempts to balance the pressure, moisture and temperature, it can specifically affect flooring systems built over unconditioned crawl spaces as the warm, moist air drives through toward the conditioned interior of the home. We call this phenomenon vapor drive.
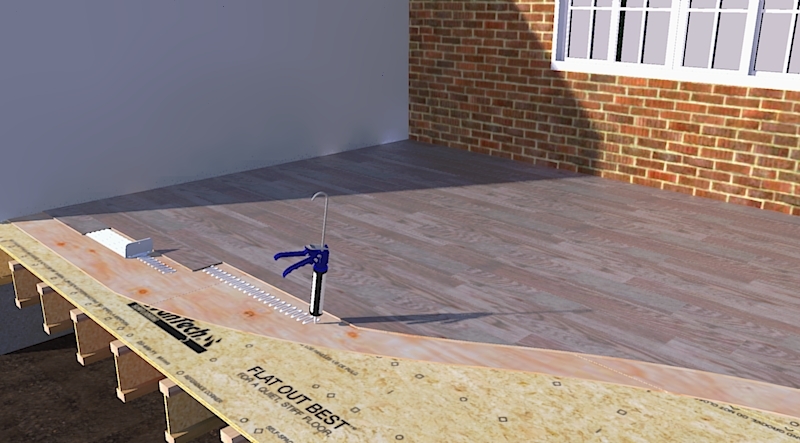
Excess moisture in a crawl space or basement is never ideal, but it becomes a problem when the moisture isn’t controlled. At Huber Engineered Woods, the Technical Hotline Support Team is seeing an increased number of questions from customers inquiring about best building practices for subfloors with luxury vinyl flooring finishes. Luxury vinyl flooring (LVF) has many positive attributes: it’s affordable, durable and an impressive alternative to more expensive finishing options.
As LVF rises in popularity, the education surrounding proper installation methods for builders will need a boost, too. Without better building techniques, we’ll almost certainly see an increase in damaged flooring.
While there are many desirable qualities of LVF, there are also some challenges. LVF installation that occurs over an unconditioned crawl space, especially in warmer, more humid climates, can significantly slow down vapor under the floor and increase the risk of condensation. The result can be bubbling, warping or cupping of the finished flooring and even cause damage to the subfloor. This can happen because of the low vapor permeability of the LVF material combined with the building methods that allow for the presence of condensation build up due to the transfer of humid air from warm to much cooler surfaces such as luxury vinyl flooring. As LVF rises in popularity, the education surrounding proper installation methods for builders will need a boost, too. Without better building techniques, we’ll almost certainly see an increase in damaged flooring.
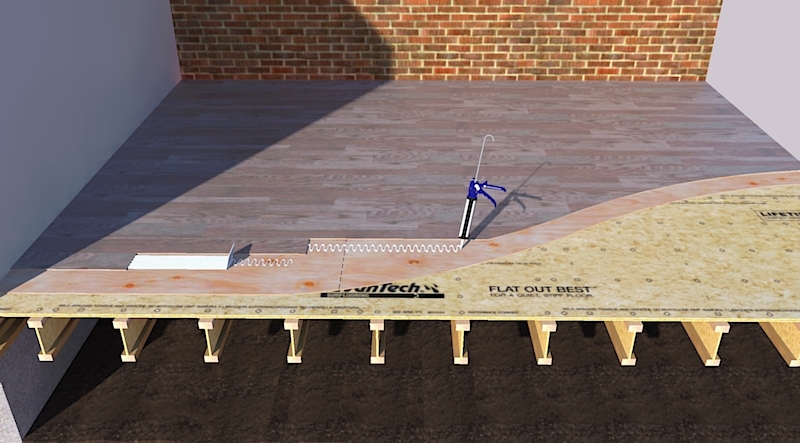
If you’re building over an unconditioned crawl space and laying LVF, here are a few considerations to promote evaporation on the underside of the flooring system to avoid condensation collection that can lead to rot:
- Always check with the flooring manufacturer for recommended installation practices. Naturally, this will vary from company to company, but some manufacturers recommend installers avoid using commodity subflooring with their luxury vinyl finished flooring. They recommend a “better” or “best” option. One reason is that the premium options, like AdvanTech subflooring, tend to be more moisture resistant, which can help prevent moisture from reaching and becoming trapped under the LVF layer.
- Inspect your crawl space for gaps in your vapor barrier on the ground and other sources of water migration. Vapor barriers should fully cover any ground and overlap at least 6”.
- Create a conditioned crawl space. Conditioned crawl spaces can prevent vapor drive and moisture build up and provide the added benefit of increased energy efficiency while still capturing the cost savings of building over a crawl space Air sealing the space is critical to control the movement of the air in a conditioned crawl space. By regulating temperature, this design takes the strain off the HVAC system, which can contribute to the home’s energy efficiency. Ultimately, a conditioned space helps avoid mold growths through more consistent climate control and can help preserve healthy indoor air quality.
- Be aware of the permeability of the materials to help promote proper drying to the exterior. If the assembly gets wet or exposed to moisture, the assembly has to have a way to dry out or a way to mitigate moisture from the onset. The building assembly is constantly adjusting under the pressure of nature seeking balance, so sequencing products with awareness of each material’s permeability will manage the vapor drive and ease this ongoing moisture movement into balance.
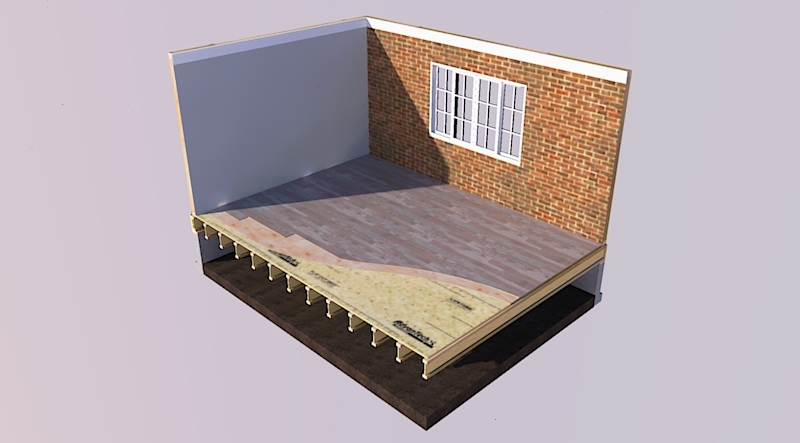
Because of the low permeability of LVF, it’s important to make sure your subflooring assembly is designed and installed to promote moisture resistance during and after construction.